Recognizing What is Porosity in Welding: Causes and Solutions
Wiki Article
Porosity in Welding: Identifying Common Issues and Implementing Best Practices for Prevention
Porosity in welding is a pervasive problem that commonly goes undetected till it creates substantial troubles with the honesty of welds. This usual issue can endanger the toughness and durability of bonded frameworks, posturing security dangers and bring about costly rework. By comprehending the root triggers of porosity and executing effective prevention techniques, welders can considerably improve the quality and reliability of their welds. In this discussion, we will check out the crucial variables adding to porosity development, analyze its damaging impacts on weld performance, and discuss the most effective techniques that can be taken on to lessen porosity occurrence in welding processes.Common Root Causes Of Porosity
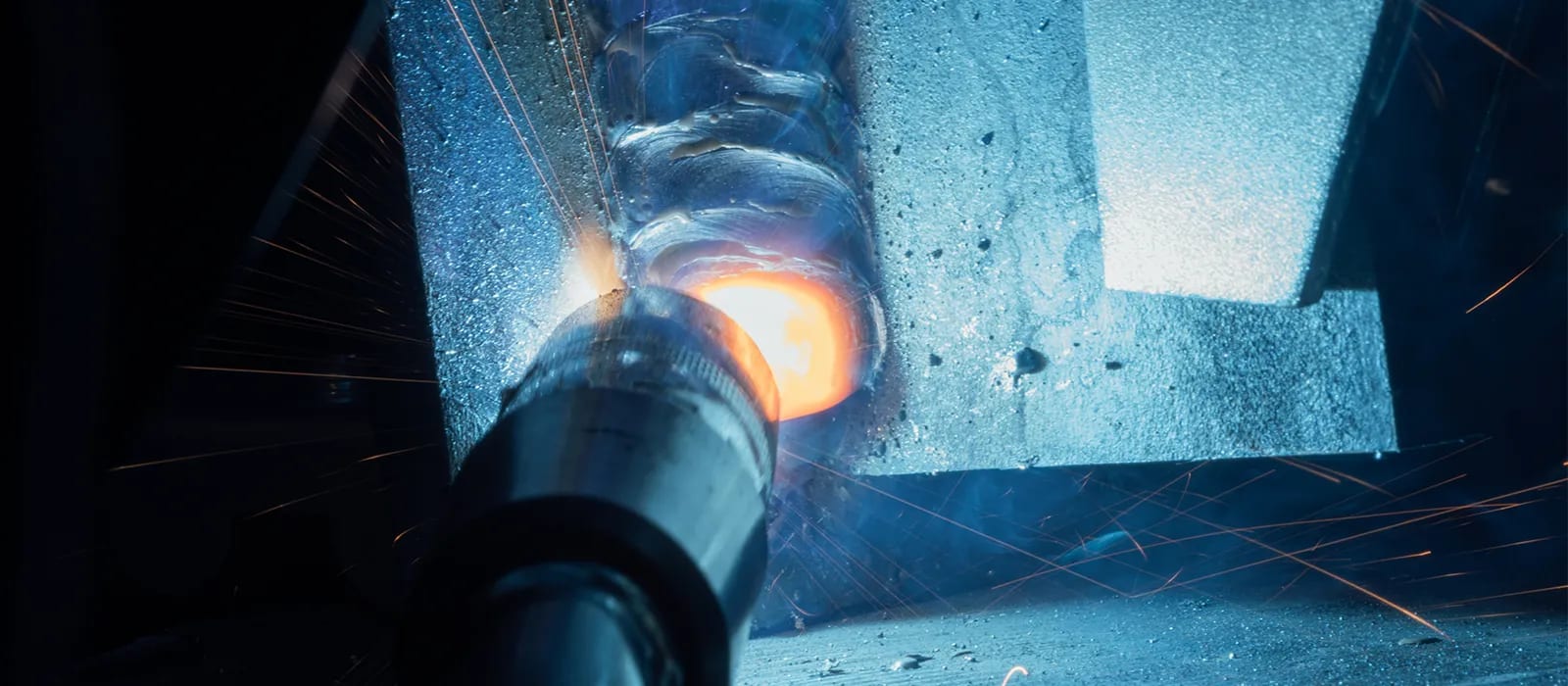
Utilizing filthy or damp filler products can introduce impurities into the weld, contributing to porosity concerns. To minimize these common causes of porosity, extensive cleansing of base steels, correct securing gas selection, and adherence to ideal welding specifications are necessary methods in achieving top notch, porosity-free welds.
Influence of Porosity on Weld Top Quality

The presence of porosity in welding can considerably jeopardize the structural stability and mechanical buildings of bonded joints. Porosity develops voids within the weld steel, weakening its overall toughness and load-bearing ability. These gaps work as stress focus factors, making the weld extra at risk to fracturing and failing under used tons. Furthermore, porosity can decrease the weld's resistance to rust and other environmental variables, better lessening its long life and efficiency.
Welds with high porosity levels often tend to show lower influence strength and minimized ability to warp plastically prior to fracturing. Porosity can hinder the weld's capacity to efficiently send pressures, leading to premature weld failing and potential security hazards in vital frameworks.
Best Practices for Porosity Avoidance
To boost the structural stability and quality of welded joints, what certain measures can be executed to decrease the occurrence of porosity throughout the welding procedure? Porosity prevention in welding is important to guarantee the honesty and toughness of the final weld. One efficient method is correct cleaning of the base metal, eliminating any pollutants such as corrosion, oil, paint, or dampness that could result in gas entrapment. Making sure that the welding tools is in good condition, with clean consumables and proper gas circulation prices, can additionally considerably decrease porosity. Furthermore, keeping a secure arc and regulating the welding parameters, such as voltage, current, and travel speed, helps produce a constant weld pool that lessens the threat of gas entrapment. Making use of the proper welding strategy for the details product being bonded, such as changing the welding angle and gun setting, can additionally stop porosity. Routine assessment of welds and instant removal of any pop over here type of problems determined during the welding process are important practices to avoid porosity and produce top quality welds.Importance of Correct Welding Methods
Carrying out correct welding methods is vital in ensuring the structural honesty and quality of welded joints, developing upon the foundation of efficient porosity avoidance measures. Extreme warm can lead to raised porosity due to the entrapment of gases in the weld pool. Furthermore, making use of the appropriate welding parameters, such as voltage, present, and take a trip rate, is crucial for accomplishing audio welds with marginal porosity.Additionally, the option of welding procedure, whether it be MIG, TIG, or stick welding, need to align with the specific demands of the job to make certain optimum outcomes. Proper cleaning and preparation of the base metal, in addition to choosing the ideal filler material, are likewise necessary parts of skillful welding techniques. By adhering to these best practices, welders can minimize the risk of porosity formation and produce premium, structurally sound welds.
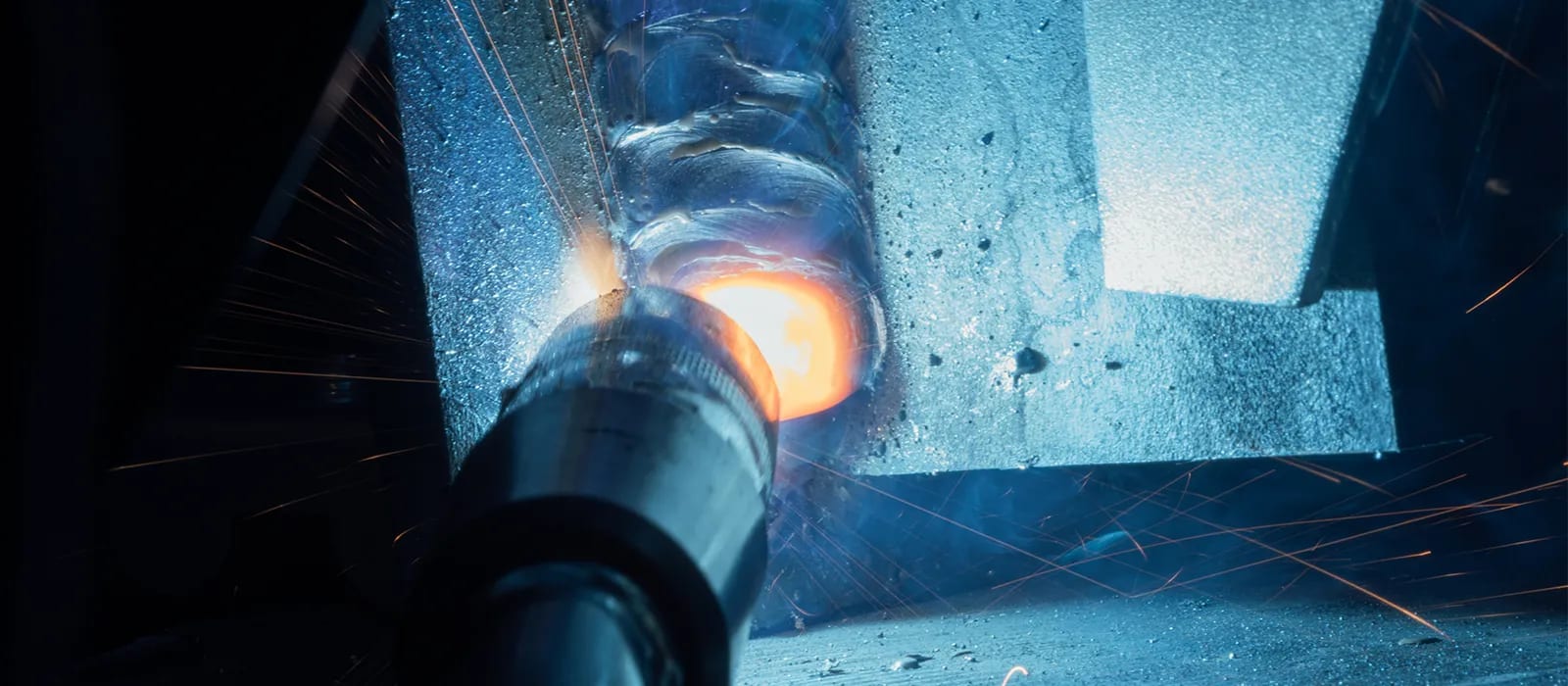
Testing and Quality Control Steps
Quality assurance measures play an essential function in validating the honesty and integrity of welded joints. Testing procedures are vital to find and protect against porosity in welding, ensuring the strength and resilience of the end product. Non-destructive testing methods such as ultrasonic testing, radiographic testing, and visual inspection are typically employed to identify potential problems like porosity. These techniques allow for the assessment of weld quality without compromising the integrity of the joint. What is Porosity.Post-weld inspections, on the other hand, analyze the final weld for any type of issues, including dig this porosity, and verify that it fulfills specified requirements. Implementing an extensive top quality control plan that includes complete screening procedures and assessments is paramount to decreasing porosity problems and making certain the general top quality of bonded joints.
Conclusion
Finally, porosity in welding can be an usual issue that impacts the high quality of welds. By recognizing the usual sources of porosity and executing finest practices for prevention, such as proper welding methods and testing procedures, welders can make certain Check Out Your URL high quality and reputable welds. It is necessary to focus on avoidance approaches to minimize the occurrence of porosity and maintain the integrity of welded structures.Report this wiki page